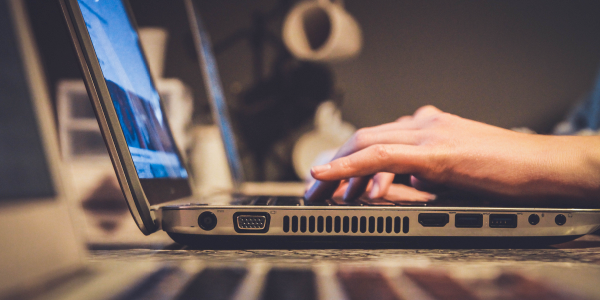
Download mount preselection software
Paulstrasoft software allows you to determine the anti-vibration solution that meets your expectations.
Download
Air compressors, which are often piston-driven, are major sources of vibration. Placed in workshops or embarked on rolling stock (trains, trucks, ships, etc.), they require the installation of low-frequency suspensions, elastomeric or metallic, which reduce the vibration levels to protect the structures and improve the acoustics of the room.
string(2) "en"